Philip Oldfield: To start, could you briefly talk about your practice, where it came from and how it evolved?
Clare Kennedy is an architect and director of design studio Five Mile Radius, which operates a workshop alongside its architecture practice. She is also involved in academia, holding various lecturing positions with universities in Australia and abroad.
Image: supplied
Clare Kennedy: Five Mile Radius is about seven years old now. We started as a group of architects who just wanted to get on the tools, but we were also very interested in where materials were coming from. We’re different from a traditional architecture practice because we are 50 percent architecture and 50 percent making. So, half the team is working more on design-based projects and half the team is in our workshop. But the two work very fluidly, hand-in-hand, which is kind of fortuitous when it comes to testing ideas about material sustainability, because we can actually just test things out ourselves.
We’re working on what are some larger projects, for us, at the moment. One’s a pub on the Sunshine Coast and it’s got a really intense time frame and budget. And that’s meant that we’ve had to really test out some of the constraints of trying to build everything with local or recycled materials.
The name Five Mile Radius has come from something Gandhi said to one of my favourite architects in India, Laurie Baker. He said: Just source stuff from the local area, within a five-mile radius of the site, because that will look after your local economy, and maintain some of the cultural traditions of an area, and design for climate, and all these great principles. So, that’s what propelled us into waste being a core conversation within the practice.
Robbie Neville is the founder of Revival Projects, a multidisciplinary practice with the ambition to make sustainable building practice more accessible to everyone.
Image: supplied
Robbie Neville: I’m a builder and my dad’s a builder and my grandpa’s a builder. When I got my builder’s licence and started taking on my own projects, I started trying to use existing resources, that I had salvaged on a really local scale, in my projects. And it was really challenging – there were so many roadblocks and so much resistance, whether it was the developer or the engineer or the design team themselves or the joiner [who] didn’t want to use recycled timber, for example. Just the notion of suggesting using existing resources was met with extreme levels of discomfort. So, I was like, “Let’s set up a business that just does that.”
But I feel now, there’s more interest than ever. There’s more appetite in the community and in the industry for that. People have to be resourceful and, in one word, that’s what we bring to the table.
Amy Seo is a co-founder of Second Edition, a research-based practice exploring deconstruction and reuse within the built environment through consultancy, design, material experimentation, prototyping and knowledge sharing.
Image: supplied
Amy Seo: We started Second Edition in earnest probably about a year ago. It’s relatively new in that sense. It came out of a response to the amount of waste that we had seen because both my business partner and I had practised in residential and commercial spaces for a while, and had seen huge amounts of waste being taken out. We wanted to firstly understand demolition practices, and it was a fact-finding mission. The demolition stage of a project is such an opaque part of the architectural process. We also wanted to get on site and get our hands dirty and to see the process for ourselves – to see why material came out the way it did and could there be a different way to do it?
We’re really interested in how we shift the architectural process – not just internally, but also to provide services for other bigger practices to implement. For instance, we could come in and under-take an existing material inventory as a starting point to help give them a tool to design from. We all have skill sets as architects. Just because we work in reuse doesn’t mean we have a different style of skill set … It’s not revolutionary, it’s just because we’re testing something that’s a little bit atypical.
PO: How do we take the practices that you’re talking about and apply them at a bigger scale? What needs to change?
RN: Well, I reckon we need a legal framework that forces the hand from the top down. I’m so tired of hearing this line: “I’m happy to do the sustainable thing, mate, but the numbers have got to add up.” The reality is that for most of the industry, that is an acceptable rationale. Why? We need laws around it, basically. Once upon a time, asbestos was legal, and now you can’t even go near it. It’s going to take the introduction of legislation to make fundamental change.
PO: Regulation is obviously vital, but do we need to demonstrate how a circular approach to materials can be faster, cheaper and more effective, as well?
CK: For the moment, it’s not cheaper. But potentially it can be, once we get suppliers, manufacturing processes and certainly some of the scientific breakthroughs that are maybe required – that should lower the price of things.
RN: You’ve raised the question of scale. I feel like we’re in a really exciting place with scale when it comes to existing resources. We’re working on some really large-scale developments at the moment and even with those, one of the first questions I’m asked is, “What’s the cost? What’s the commercial reality of this?” And if I couldn’t demonstrate an immediate commercial upside, I wouldn’t have got the traction that we’ve got on the larger projects.
And then the bigger picture. Talking about sustainability and the built form, you know you will reach a point where you have to accept that if you want do things more sustainably, you don’t get to choose the pace and you don’t get to choose the specifics. I think we have to become comfortable with compromising on some of the things that we’ve come to take for granted as being entirely our choice. For example, we don’t design and nominate the spec or a finish because [the client] might like the look of it. The question we need to ask is: What are the resources we’ve got access to that are sustainable? Let that inform the design development.
PO: We are an incredibly risk-averse industry. How do you navigate that space with reused and recycled materials?
AS: We’re working through some of that at the moment for specifying glass that’s excess stock from skyscrapers. It’s all custom systems, so fabricators have to make a certain set percentage over and hold it for a number of years in the event that the building gets damaged. Those years end, and they have a warehouse filled with glass. I was there this morning and we’re trying to work out the certifications required. Who actually certifies it? Sometimes, there’s multiple ways to tick a box, and it’s like, how do we explore those options?
Offcut Kitchen by Second Edition is made from fibre-reinforced plastic, a material commmonly used for walkways.
Image: Hamish McIntosh
RN: We’ve got a large adaptive reuse project on the go at the moment. We’ve been on site for a year and a half. We had to demolish certain aspects of the building and we salvaged a lot of old Victorian ash and Oregon timber. We’ve used the recycled timber as stair treads – that sounds fairly simple, but we’ve needed a friend in the accessibility consultant, and we’ve needed a friend in fire engineering. We worked very closely with the building surveyor to table the right documents that talk about smoke-spread rate for these particular timber species. (If they catch fire, how do they stack up compared to other timbers that have a nice little data sheet and certificate that comes with them when you buy them off the shelf?) If we didn’t have that support network of the right consultants, then it wouldn’t have been considered for five seconds. You can’t expect an architect on their own or a builder on their own to have that understanding of those different considerations that are necessary for compliance. So, you need a collaborative support network.
PO: To wrap up, can you highlight one thing that every practice could action to improve material waste in the built environment?
CK: What people could do is use every project and opportunity to explore something that looks at a more respectful use of resources. I don’t think you need to do it across 100 percent of the materials within a project, but if you do it across five, you’ve helped spur on the industry. Architects shouldn’t be defeatist and say, “Oh, we’re not getting things across the line.” Keep trying.
Telegraph stool (left) and Waste Terrazzo (right) by Five Mile Radius.
Image: Callie Marshall
AS: It’s always just assessing the existing material stock. So long as we learn from one project and then build on that and understand what worked and what didn’t, and try it again … it’s being persistent. Just staying positive and having a collegiate attitude is really important, and also ensuring that knowledge is shared.
RN: Adopt an approach of custodianship over consumption. When we adopt things as custodians, they’re ours to look after and then pass on to the next person. Earlier this year, we launched the Urban Tree Recovery Initiative. And very quickly, we’ve been inundated with trees that people have no use for. So, we’ve got this resource now and we’re channelling it out into the industry via transfer-of-custody agreements. Nothing is sold. We don’t reduce the resource to a commodity and give it a price tag and make that the singular criteria for the exchange. We have a transfer-of-custody agreement, and it introduces a set of principles and responsibilities. I suppose there’s a duty of care introduced so that you’re not just expected to pay the money and then do whatever you want with it and consume as much as you like.
It’s so exciting. It feels like a really liberating step forward.
Source
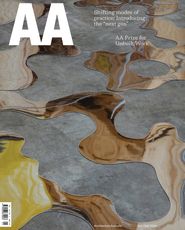
Discussion
Published online: 5 Feb 2024
Words:
Philip Oldfield
Images:
Callie Marshall,
Hamish McIntosh,
Sean Fennessy,
supplied
Issue
Architecture Australia, January 2024