The start of the 2020s has seen extreme environmental and economic pressures reshape the way we think, live and work. In a similar manner to architecture’s postwar era, our buildings are responding to – and becoming timestamps of – the present context. The University of Queensland Cricket Club Maintenance Shed, by Lineburg Wang with Steve Hunt Architect, is a small project located in Meanjin/Brisbane that marks a moment in time. Developed over 2021 and 2022, the scheme battled constant cost revisions in response to shortages of labour and materials, which had been rightfully redirected to rebuilding homes lost in the 2022 floods across Queensland and New South Wales. These external factors morphed the building into what it is today: a clever, functional structure that is a prime example of the value of architects.
So, why go to all this effort instead of simply installing a stock-standard shed? It would be easy to assume that the site, nestled between the existing cricket clubhouse and practice nets, is largely hidden from view. However, located within the first hundred metres of one of the university’s informal entry points and overlooked by colleges, this building is for some the first impression of the university before arriving at the Great Court that is the heart of the St Lucia Campus. “This could not be an ordinary back-of-house shed because this building is actually quite prominent on the ring road [Sir William MacGregor Drive], and it really becomes the new face of the cricket club,” shared Michael Lineburg. To match the reputation of the university and the pride of the cricket club, this “back-of-house” building – which is the first stage of the club’s masterplan – needed to add value in more ways than one.
What could have been a stock-standard shed has become a pleasing and practical structure upheld by a rigorous design.
Image: David Chatfield
The UQ Cricket Club, established in 1912, has had its fair share of “skippers.” When Steve Hunt, Lynn Wang and Michael Lineburg were engaged to work on the project in 2016, the club facilities – one toilet between two change rooms – had been neglected for decades and were far from sufficient for the number of users. But the budget was low. From the beginning, the main design driver was the required program: a bathroom, a toilet block and a storage space for equipment, tractors and chemicals. “Given the functions required of the building, it made sense that it was not sealed … It was exciting for us to think about just a line of security and two functions that are separated by a courtyard,” said Wang. As a result of the architect’s quest to avoid using whirlybirds to ventilate the building, the facade became a direct outcome of the interior program. But the shed’s perforated skin – made from standard grey breezeblocks – is more than a functional, cost-saving device; its intriguing form enhances the streetscape.
For cost-effectiveness, the first iterations of the shed were designed to be lightweight. But with storm reconstruction work and other major infrastructure developments across the state inflating the cost of steel, the architects had to remove as much of the material as possible.1 They reduced the length and volume of the initial scheme, but prices continued to increase, making off-the shelf lightweight construction infeasible. “The builder literally said the only thing you can use is standard grey block,” explained Wang.
Prominently positioned on the ring road at the campus’ edge, the shed has an intriguing facade that is both decorative and cost-saving.
Image: David Chatfield
Wondering how they could use blocks to create a facade that was more than decorative, Lineburg Wang worked closely with the engineer. The solution came from pushing the boundaries of block-laying. The facade uses standard three-quarter blocks on a standard 400-millimetre grid to create points of perforation. A typical lintel block is then flipped on its side to create the recessed horizontal lines on the exterior face. This strategy ticked the box for retaining an open facade and removed a significant amount of steel. The next challenge was how to make this heavy skin structurally sound.
At the time, some members of the project team were concerned about the structural soundness of a lintel that was turned on its side. “Theoretically, [the lintel] should snap at this point … but because of the engaged piers and how [often they occur], the lintel blocks aren’t actually taking on any load,” said Wang. Every third block extends back by 400 millimetres and is then core-filled with concrete, which zigzags down to become an engaged pier that holds up the facade. Unlike a column, the engaged pier is structurally united with the skin of the building; neither can be value-managed out.
This intensive collaboration demonstrates the architect’s ability to synthesize ideas and find solutions, even for the smallest of buildings and budgets. As Hunt shared, “There was complexity in executing something so simple … [and] it took a level of intent, rigour and self-advocacy.” What could have been a typical blockwork building, similar to the standard amenities built in many parks in the eighties and nineties, became something refreshingly different thanks to the architect’s dedicated pursuit of a better outcome that still meets the requirements of client, project team and end user. According to Wang, “It’s about not being precious in your own architectural ideas. As architects, we have a role where we can be creative but also use the project’s constraints to deliver an outcome that meets the client’s brief.”
As the result of intensive collaboration between architect, engineer and builder, the project expresses new approaches to standard building materials.
Image: David Chatfield
Paramount to this project was the level of precise detailing required to ensure that the illusion of this concrete weave, sitting among the gumtrees, was not interrupted by carelessly placed services protruding from its skin. The result is a testament to the architect’s time spent on site, engaging intensely with contractors and builders, experimenting with materials and building 1:1 details.
A high level of on-site engagement and collaboration is a distinguishing feature of the next generation of architects, including Steve Hunt Architect and Lineburg Wang. This could be a partially circumstantial matter, as smaller practices tend to have greater flexibility to be on site. But additional external pressures, including unstable economies and increasingly extreme climatic changes, are prompting explorations into new materials and construction methods that are only effective if undertaken on site alongside the relevant manufacturers, contractors and consultants.
The UQ Cricket Club Maintenance Shed demonstrates how even the smallest of projects is shaped by current affairs. As Lineburg Wang and Steve Hunt Architect’s first public building, the project has been a challenging yet worthwhile journey. This humble shed, which won an Australian Institute of Architects’ National Award for Small Project Architecture in 2023, is a testament to architectural thinking, resilience and pursuit.
- According to the CBRE’s construction report, in the year to July 2022, the cost of structural steel increased by 39.5 percent per tonne and the cost of labour spiked; see cbre.com.au/press-releases/construction-cost-price-escalations-in-australia-expected-to-peak-in-2022.
Credits
- Project
- University of Queensland Cricket Club Maintenance Shed
- Architect
- Lineburg Wang
Brisbane, Qld, Australia
- Project Team
- Lynn Wang, Michael Lineburg, Steve Hunt, Chris Kotmel
- Architect
- Steve Hunt Architect
Qld, Australia
- Consultants
-
Blocklayer
Armstrong Bricklaying
Builder Xenia Constructions
Certifier McKenzie Group
Hydraulic engineer Neil Blair and Associates
Structural engineer Ingineered
- Aboriginal Nation
- Built on the land of the Turrbal and Yuggera people.
- Site Details
- Project Details
-
Status
Built
Type Infrastructure, Small projects
Source
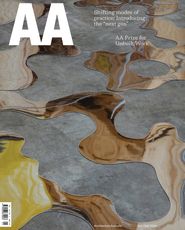
Project
Published online: 5 Mar 2024
Words:
Georgia Birks
Images:
David Chatfield
Issue
Architecture Australia, January 2024